Mountboard chevron display methods
-
- Posts: 11004
- Joined: Sat 25 Mar, 2006 8:40 pm
- Location: Devon, U.K.
- Organisation: The Dartmoor Gallery
- Interests: Lost causes, saving and restoring old things, learning something every day
- Location: Glorious Devon
Mountboard chevron display methods
I am intending to produce some new display units for my mountboard chevrons. I've got a few thoughts and ideas which are still developing, but I am probably going to produce a revolving display mounted on a "Lazy Susan" type rotating bearing, with colours separated into groups to make the whole selection process more customer friendly.
The intention is to have a few of these units kept behind the counter, so that the customer only needs to have the most appropiate unit on hand so as to make the process less confusing to the struggling customers which we all get at times.
I think this might be an interesting subject for discussion, which perhaps could be broadened, if necessary to take in other related matters, such as how we handle this part of the customer consultation process.
The intention is to have a few of these units kept behind the counter, so that the customer only needs to have the most appropiate unit on hand so as to make the process less confusing to the struggling customers which we all get at times.
I think this might be an interesting subject for discussion, which perhaps could be broadened, if necessary to take in other related matters, such as how we handle this part of the customer consultation process.
customer - consultation? you mean you offer more than two mount colours?
to be serious - Lion do a very handy chevron display - holds 40 chevrons. As for consultation - I like my customer to think they have made a good choice - I am there to guide - ask questions - point out obvious choices. The customer has to trust you. I like people and I like talking to my customers and often think the initial sale is the best part of the job.
How many times have you had customers go through every conceivable mount / frame combination only to come back to the one you suggested first? frustrating - but patients and a desire to serve your customer has to be an important part of that consultation process - better to spend time selecting than consoling when they don't like the finished product.
to be serious - Lion do a very handy chevron display - holds 40 chevrons. As for consultation - I like my customer to think they have made a good choice - I am there to guide - ask questions - point out obvious choices. The customer has to trust you. I like people and I like talking to my customers and often think the initial sale is the best part of the job.
How many times have you had customers go through every conceivable mount / frame combination only to come back to the one you suggested first? frustrating - but patients and a desire to serve your customer has to be an important part of that consultation process - better to spend time selecting than consoling when they don't like the finished product.
I made two such devices a few years ago. The panels are six feet high on a one foot base. There are four panels that form a cross shape when looking down from the top so that makes eight surfaces to place chevrons on. (It sounds so posh when people say or type "chevrons")
On average, each side will hold about 36 chevrons, so a total of 288 on each unit and 576 on two. I also have some wall space, but still not enough space to hang all the chevrons I want.
I can take and post a photo if anyone wants!
On average, each side will hold about 36 chevrons, so a total of 288 on each unit and 576 on two. I also have some wall space, but still not enough space to hang all the chevrons I want.
I can take and post a photo if anyone wants!
-
- Posts: 313
- Joined: Tue 12 Sep, 2006 6:46 pm
- Location: Netley Marsh New Forest Hampshire
- Organisation: Hampshire Framing
- Interests: Golf, DIY and baking bread,cakes, biscuits and making chilli jams and various chutneys.
- Location: NEW FOREST HAMPSHIRE
I think the initial consultation and choices made by you with the customer is extremely important. For them to have implicit confidence in your judgement and ability to guide through what may seem a myriad of colours and styles.
Number 1 rule: never let the customer loose on the mount display or the framing board. Absolutely fatal; seen it happen, wastes time and you lose control.
Given a choice of say three or four mouldings and a couple of mounts, I often find the first off the board is the one we nearly always come back to.
I group mount colours light to dark on a flat board on the wall behind the counter. Reds and hot colours together; blues and cooler colours likewise, and whites through to ivories and buffs also. They can be seen at once by everyone and a small selection made without scrabbling through a swatch stack on the counter. The slicker you can make selection the better.
Number 1 rule: never let the customer loose on the mount display or the framing board. Absolutely fatal; seen it happen, wastes time and you lose control.
Given a choice of say three or four mouldings and a couple of mounts, I often find the first off the board is the one we nearly always come back to.
I group mount colours light to dark on a flat board on the wall behind the counter. Reds and hot colours together; blues and cooler colours likewise, and whites through to ivories and buffs also. They can be seen at once by everyone and a small selection made without scrabbling through a swatch stack on the counter. The slicker you can make selection the better.
Measure twice - cut once
-
- Posts: 11004
- Joined: Sat 25 Mar, 2006 8:40 pm
- Location: Devon, U.K.
- Organisation: The Dartmoor Gallery
- Interests: Lost causes, saving and restoring old things, learning something every day
- Location: Glorious Devon
Foxyframer,
Yes, I agree with your ideas for grouping colours. By seeing the contents of each group at a glance and then working within that group, just seems to be the smart thing to do.
It drives me nuts when someone wants to mess around for hours pulling out all the mount chevrons. This is because the normal display caddy packs them all into the minimum space and they can't been seen.
The idea behind the revolving display is that it can turned to show one group of colours at a time and all the colours within that group are immediately visible at the start.
Yes, I agree with your ideas for grouping colours. By seeing the contents of each group at a glance and then working within that group, just seems to be the smart thing to do.
It drives me nuts when someone wants to mess around for hours pulling out all the mount chevrons. This is because the normal display caddy packs them all into the minimum space and they can't been seen.
The idea behind the revolving display is that it can turned to show one group of colours at a time and all the colours within that group are immediately visible at the start.
-
- Posts: 11004
- Joined: Sat 25 Mar, 2006 8:40 pm
- Location: Devon, U.K.
- Organisation: The Dartmoor Gallery
- Interests: Lost causes, saving and restoring old things, learning something every day
- Location: Glorious Devon
I wanted to do something with Lions individual 20 chevron panels from the same product on a four or more sided revolving display. I also remember that a few years ago Nielsen Bainbridge offered a display which took four or five grouped chevrons in each slot. They don't appear to do it now.markw wrote:Lion do a very handy chevron display - holds 40 chevrons.
One of the difficulties I find is customers who come in, but only have limited time. I want to make the process easier for these customers so that they don't end up saying that they've run out of time.
-
- Posts: 313
- Joined: Tue 12 Sep, 2006 6:46 pm
- Location: Netley Marsh New Forest Hampshire
- Organisation: Hampshire Framing
- Interests: Golf, DIY and baking bread,cakes, biscuits and making chilli jams and various chutneys.
- Location: NEW FOREST HAMPSHIRE
NYA
Time: I can fully sympathize with you on those who simply don't allow enough time.
All the product of todays' rush ass mentality.
Regulars have a fair idea how long a consultation takes; put enough money in the meter and are prepared to take time. Ours is a relaxed and easy atmosphere and that's how it should be.
As a reflection of this: you're busy serving, a couple come in with a pic, can't wait patiently or look around and make straight for the framing board. 'Be with you shortly'. You can see them out of the corner of your eye making some horrendous choices.
Left to themselves it would be a complete nightmare.
Time: I can fully sympathize with you on those who simply don't allow enough time.
All the product of todays' rush ass mentality.
Regulars have a fair idea how long a consultation takes; put enough money in the meter and are prepared to take time. Ours is a relaxed and easy atmosphere and that's how it should be.
As a reflection of this: you're busy serving, a couple come in with a pic, can't wait patiently or look around and make straight for the framing board. 'Be with you shortly'. You can see them out of the corner of your eye making some horrendous choices.
Left to themselves it would be a complete nightmare.
Measure twice - cut once
-
- Posts: 11004
- Joined: Sat 25 Mar, 2006 8:40 pm
- Location: Devon, U.K.
- Organisation: The Dartmoor Gallery
- Interests: Lost causes, saving and restoring old things, learning something every day
- Location: Glorious Devon
Foxyframer,
I don't mind spending the time, but I get cheesed off with customers who can never make up their minds and after wasting one or even two hours, decide to come back when they have more time. They rarely do! Couples often are the worst, especially when they can't agree between themselves.
However I've come to the conclusion that a visually helpful mountboard display is a good first step to improving the whole process.
I've included a scan of a small portion of an old Nielsen Bainbridge publication which shows their approach to this at that time. I have no idea how old this is, but it's not shown in any recent publications. (All rights concerning this image are the property of Niesen Bainbridge).
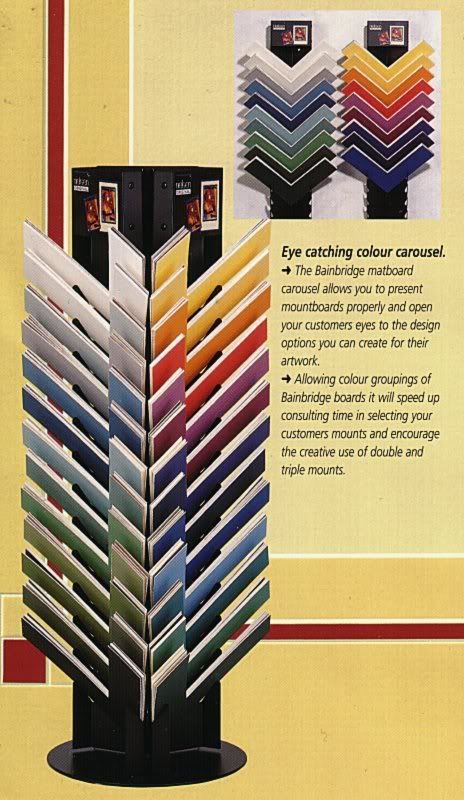
As you will see, if look carefully the mountboard samples are not displayed singly, but in small colour related groups.
I don't mind spending the time, but I get cheesed off with customers who can never make up their minds and after wasting one or even two hours, decide to come back when they have more time. They rarely do! Couples often are the worst, especially when they can't agree between themselves.
However I've come to the conclusion that a visually helpful mountboard display is a good first step to improving the whole process.
I've included a scan of a small portion of an old Nielsen Bainbridge publication which shows their approach to this at that time. I have no idea how old this is, but it's not shown in any recent publications. (All rights concerning this image are the property of Niesen Bainbridge).
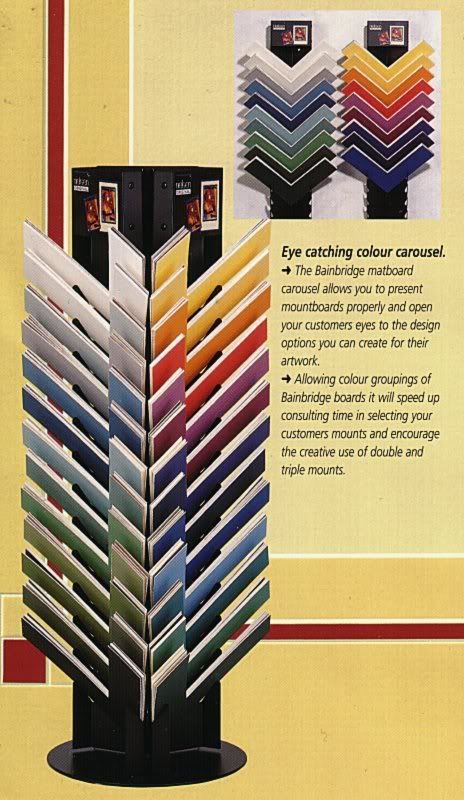
As you will see, if look carefully the mountboard samples are not displayed singly, but in small colour related groups.
I've got one of those spinners - use it for slips (fillets) attached to mount chevrons and special finishes such as fabric and washlined mounts.
Prefer my main selection on caddies - easier to put back in order - just draw a line in felt pen from top left to bottom right along the edges of the boards. Find this easiest when helping cutomers choose too.
Prefer my main selection on caddies - easier to put back in order - just draw a line in felt pen from top left to bottom right along the edges of the boards. Find this easiest when helping cutomers choose too.
-
- Posts: 11004
- Joined: Sat 25 Mar, 2006 8:40 pm
- Location: Devon, U.K.
- Organisation: The Dartmoor Gallery
- Interests: Lost causes, saving and restoring old things, learning something every day
- Location: Glorious Devon
Hi John,Roboframer wrote:Prefer my main selection on caddies - easier to put back in order - just draw a line in felt pen from top left to bottom right along the edges of the boards. Find this easiest when helping cutomers choose too.
I should have thought of that, but I didn't. I like the sound of that, I bet with a little practice you get to know where to grab the exact chevron you wanted straightaway.
Nice one John, I might just be re-thinking my ideas after this!
If you have your corners sorted into colour wheel sets (Alphamat has this on the back of each corner) you can use a band of felt pen, or two, in the same colours as each set. ie. red felt pen on the red set, a red and an orange band on the red-orange set, blue band and green band on the blue-green set, etc, etc.Roboframer wrote: just draw a line in felt pen from top left to bottom right along the edges of the boards.
Mountboard display units
We have our matt-board corner samples grouped by colour on an "A" shaped product holder supplied by one of the manufacturers - we don't attempt to keep them in any order other than the selected colour code. We use a mixture of Crescent, the old Tru Vue and Watermark matt-boards with the Crescent Rag matt-board samples on a separate holder. We don't use all matt-board samples provided, preferring to select the colours we use( the factory is still full of matt-board offcuts but we are weeding out those boards that only get used once in a blue moon!). We stock take every 6 months and thereafter cull/add to the range of samples as required, based on the preceeding 6 months usage
When working with a customer, we aim to show them a double matt combination - after initial discussions to ascertain what the customer is looking for we lay out suggested matt combinations, but at all times, the customer can see a fanned out range of colours in thoses selected so that they can see the options
Some will want to play with a multitude of colours, but as someone else has said on another posting it is amazing how often we are told you were right the first time!
I can't see the point in having the matt corner samples on display where customers can view the whole colour range like the photo image earlier. In my opinion, people come to a custom framer seeking professional advice, and through a consultative process we talk to the customer, we engage them in all aspects of a custom framing job including the matt-board selection and to our knowledge they are satisfied with the end product.
It rarely happens, but if a customer is not a 100% happy with the finished product we will revisit the whole project and make any changes that they may want - would not have done this for more than 2 years
When working with a customer, we aim to show them a double matt combination - after initial discussions to ascertain what the customer is looking for we lay out suggested matt combinations, but at all times, the customer can see a fanned out range of colours in thoses selected so that they can see the options
Some will want to play with a multitude of colours, but as someone else has said on another posting it is amazing how often we are told you were right the first time!
I can't see the point in having the matt corner samples on display where customers can view the whole colour range like the photo image earlier. In my opinion, people come to a custom framer seeking professional advice, and through a consultative process we talk to the customer, we engage them in all aspects of a custom framing job including the matt-board selection and to our knowledge they are satisfied with the end product.
It rarely happens, but if a customer is not a 100% happy with the finished product we will revisit the whole project and make any changes that they may want - would not have done this for more than 2 years
Ross,
Sorting corners by colour wheel groups will simplify and speed up your process to find the right colours. I saw it first at a trade show in the late 80's and have used this method ever since. I would never go back to any other method. It saves time and time is money!
If the brands that you use don't have this info on the back, you could get a set of Alphamat samples and use that to help sort all the other brands.
I tried Watermark many years ago and dumped it immediately due to all the bits of grit in it. Does it still contain grit that blunts three or four blades per opening?
Sorting corners by colour wheel groups will simplify and speed up your process to find the right colours. I saw it first at a trade show in the late 80's and have used this method ever since. I would never go back to any other method. It saves time and time is money!
If the brands that you use don't have this info on the back, you could get a set of Alphamat samples and use that to help sort all the other brands.
I tried Watermark many years ago and dumped it immediately due to all the bits of grit in it. Does it still contain grit that blunts three or four blades per opening?
Ormond
Watermark matts are probably a little harder on blades, but not to the extent you highlight
You make mention of Alphamats - why are they so much better than the crescent rag series. One can not change matt-board supplier at the drop of a hat if you maintain a reasonable supply of boards in stock and not have to reorder every time one is required
If I understand what you have said, the Alphamat has a number of references on the back of each sample to identify there relationship to the colour wheel (used by designers) - I requested the current specifiers for the Alphamats, but couldn't find a reference to this subject during a fleeting review, so will have to find the colour wheek and then try to gain an understanding of this issue
By way of interest, how many framers reading this make any use of the colour wheel in their business?
I don't understand what drawing a line on the back of one's corner samples achieves, other than a useful tool to keep samples within colour groupings - surely they are not designed to have corner samples in a precise colour order - if that is the case, then one must have to sort them after every use if the samples
Ross
Watermark matts are probably a little harder on blades, but not to the extent you highlight
You make mention of Alphamats - why are they so much better than the crescent rag series. One can not change matt-board supplier at the drop of a hat if you maintain a reasonable supply of boards in stock and not have to reorder every time one is required
If I understand what you have said, the Alphamat has a number of references on the back of each sample to identify there relationship to the colour wheel (used by designers) - I requested the current specifiers for the Alphamats, but couldn't find a reference to this subject during a fleeting review, so will have to find the colour wheek and then try to gain an understanding of this issue
By way of interest, how many framers reading this make any use of the colour wheel in their business?
I don't understand what drawing a line on the back of one's corner samples achieves, other than a useful tool to keep samples within colour groupings - surely they are not designed to have corner samples in a precise colour order - if that is the case, then one must have to sort them after every use if the samples
Ross
Ross,
Alphamats are better, mainly because the have "zeolytes" in them. This is a substance that traps harmful gases inside the frame package. there is no doubt that Crescent Rags are a great matboard, but if another brand (Alphamat) has any advantage, it's my opinion that it should be considered so that you can gain that extra benefit.
Another advantage, in my opinion is that Alphamats are stiffer, less flexible and I like that.
It is difficult to change brands , but it can be done reasonably easily. Just show your customers the Alphamat samples and the Crescent Rag samples of the boards you have in stock. As they are used up, don't show them.
The specifiers don't have the colour wheel info on them, only the corner samples. I recently got a whole new set of Alphamat corners which I cut bevels on and I have them in my caddies in colour wheel sets and in an approximate order from lightest to darkest.
I have all the different styles in together and this enables me to sell all the different price brackets. I also include suedes in the rack, even though they are not Alphamat and find that this helps to sell them too.
The diagonal line on the edge, in the colours of each set enables me to put them back in their place easily and in a very short time. Having them sorted this way means that I don't have to get a million samples out of the rack for any one design.
By nature I am not a very organised person, but this is one area that I find great advantage in being organised well.
Next week I will take a photo of my sample caddies and email it to you if you wish to see what it looks like.
Alphamats are better, mainly because the have "zeolytes" in them. This is a substance that traps harmful gases inside the frame package. there is no doubt that Crescent Rags are a great matboard, but if another brand (Alphamat) has any advantage, it's my opinion that it should be considered so that you can gain that extra benefit.
Another advantage, in my opinion is that Alphamats are stiffer, less flexible and I like that.
It is difficult to change brands , but it can be done reasonably easily. Just show your customers the Alphamat samples and the Crescent Rag samples of the boards you have in stock. As they are used up, don't show them.
The specifiers don't have the colour wheel info on them, only the corner samples. I recently got a whole new set of Alphamat corners which I cut bevels on and I have them in my caddies in colour wheel sets and in an approximate order from lightest to darkest.
I have all the different styles in together and this enables me to sell all the different price brackets. I also include suedes in the rack, even though they are not Alphamat and find that this helps to sell them too.
The diagonal line on the edge, in the colours of each set enables me to put them back in their place easily and in a very short time. Having them sorted this way means that I don't have to get a million samples out of the rack for any one design.
By nature I am not a very organised person, but this is one area that I find great advantage in being organised well.
Next week I will take a photo of my sample caddies and email it to you if you wish to see what it looks like.
Hi Ormond
Thanks for the recent advices - would appreciate the e-mail you refer to
When you have v-grooves on every matt sample, is there a tedancy to oversell something that I think works sometimes but not on everything. I find v-grooves are often distracting and don't know if I could work with them on all my samples
Ross
Thanks for the recent advices - would appreciate the e-mail you refer to
When you have v-grooves on every matt sample, is there a tedancy to oversell something that I think works sometimes but not on everything. I find v-grooves are often distracting and don't know if I could work with them on all my samples
Ross